The Pros and Cons of Drywall
Pros and Cons of Drywall
Getting the appropriate building materials is critical whether you're constructing a new building or remodeling an existing one. The ceilings and walls should be sturdy and long-lasting. Furthermore, keep in mind that people consider these as permanent structures. Drywall installation is famous for both ceilings and walls.
While there are benefits and drawbacks to drywall, the positives appear to exceed the negatives. As a result, the manufacture of most residential and commercial walls and ceilings are now drywall. Regardless, knowing the benefits and drawbacks of drywall can help you make more educated judgments about construction materials.
What is Drywall?
Drywall is a non-loading bearing ceiling and wall material utilized to construct partitions. The use of this material is also to make things like conduits, culverts, arches, ducts, drains, and other architectural features. It's quick and straightforward to put together, quite sturdy, and only requires minor repairs if broken.
It is also an excellent material for installing access doors and panels to enable your maintenance personnel to gain entry into your utility areas. If you plan to install some for your building, ensure to talk to a professional first, especially if the hatch goes up to your roof area. They might advise you also to set up a
roof hatch safety railing to comply with regulations.
Professionals use this material to wrap columns in commercial buildings to hide steel beams and is an efficient and affordable technique to finish masonry walls above ceilings. Another application of drywall is to increase fire protection to ceilings and walls, allowing people to evacuate safely in case of a fire.
Why Use Drywall?
Building interiors or internal walls were built of masonry with plaster before drywall became commonly utilized. The construction of walls and ceilings have always been through the layering wet plaster material over vast numbers of timber strips called laths or masonry, typically brick or stone, for hundreds of years.
The liquid plaster mortar would eventually solidify to create walls, but the installation and maintenance methods were inefficient and challenging to master. As a result, plastering walls needed many applications, each with a lengthy drying period in between. In addition to its protracted installation time, plaster application was very labor-intensive, requiring experienced artisans to labor over a tiny portion of a wall for weeks until its completion.
Finishing walls might take weeks with plaster, but it can be in a matter of days using drywall, and they would endure longer and cost less to build in some locations. You can repair damaged drywall more quickly and efficiently than plaster. It also offers a higher level of fire resistance and evenly polished, linear, and leveled surfaces.
Despite these advantages, builders are hesitant to adopt drywall, primarily due to expense, as it is still more expensive than a traditional wall.
The Advantages
The following are the upsides of using drywall in a construction project:
The manufacturing of drywall is quicker, which reduces the energy expenses associated with its creation.- Even though drywall is a heavy material, a skilled drywall contractor with the proper lifting machinery and equipment can quickly construct ceilings or walls, which results in a quick installation.
- The fact is that drywall isn't exceptionally long-lasting. Although it is a drawback, it is reasonable to assume that drywall plastering will significantly strengthen the surface.
- The gypsum in drywall makes it fire-resistant, preventing the fire from spreading.
- It's a budget-friendly option.
- You can easily install recessed lights and hang whatever you want with drywall ceilings and walls.
- It has a consistent appearance over its whole surface.
- Installation does not necessitate the use of water; thus, the site remains clean and neat.
- You may use it to build standard ceilings, walls, and partitions, among other things.
- It's simple to remove and reinstall, and it comes in a variety of sizes. It implies you can hide a hole with drywall by removing a piece and fitting it to the spot.
- You get consistently smooth surfaces with no undulations, and they're perfectly straight and level, which is challenging to do with regular plaster on a brick wall.
- Normal shrinkage and creep cracks in standard brick or stone walls with cement plaster are not present.
The Disadvantages
Here are the downsides of using drywall in a construction project:
Although drywall is relatively simple to install, specialists and technicians must qualify for drywall installation. Finishing requires the correct procedure, or you may get difficulties with the seams or tapes afterward. They also must prepare the area before the installation since drywall produces a lot of dust, which may quickly travel throughout the building.- Because drywall is not soundproof on its own, you may need sound insulation between the two layers.
- Damage to the drywall surface is typical. Because drywall is not impact-resistant, you may destroy it quickly. As a result, you may encounter issues such as holes, densely damaged corners, tapes coming loose, and joints splitting. The excellent news is that you may resolve these issues with drywall repair.
- As a general rule, drywall is not water-resistant. It will suffer damage if you put it in high-moisture areas like bathrooms or basements. Mold infections thrive in wet walls. If your drywall has suffered damage from water exposure, you'll need to repair it. The only way to solve the problem is to use fiberglass drywall instead of paper. These kinds of drywall are more resistant to water.
- You cannot erect drywall independently because it necessitates the use of steel, wood, or MS framing.
- You cannot use drywalls for external walls unless it undergoes specific water-resistant treatments. You can, however, utilize them for interior areas.
- You cannot install plumbing, electric, and sound insulation on the surface of drywall; you must do it between two sheets of drywall.
The Manufacturing Process
Gypsum is the most common material used in the construction of drywall. Gypsum is a mineral you can typically find in huge earth beds that resemble white sand; however, impurities can make the beds seem yellow, pink, or grey. New Mexico's White Sands National Monument is one of the most well-known gypsum beds in the United States.
The crystalline gypsum contains a considerable quantity of water, so the individual gypsum molecules are dry. As the drywall heats up, the water crystals collapse and begin to vaporize as the water heats up to its boiling point. It keeps the drywall cold by evaporating water crystals, which protects the structure underneath it. As a result of this characteristic, it makes drywall a fire-resistant material.
After the mining process, gypsum goes to factories. After the transportation, it undergoes a process of mixing with numerous additives such as paper pulp, starch, and thickening agent or emulsifier before being blended with water to produce a thick paste. The manufacturer will then apply it to Manila paper layers of 3/8-inch (8 mm) to 3/4-inch (20 mm) thickness. It will then have another sheet of Manila paper on top of it.
The entire structure goes in the furnaces to temperatures as high as 500 degrees Fahrenheit. It dries the cloth and makes it ready to cut. Typical sheets are 48 feet long; however, 410 and 412-foot sheets are gaining popularity since they enable speedier installation of higher walls.
Drywall is such a fantastic construction material, and its application to many buildings makes it worthy of consideration. There are many drywall types, and it would be best for you to consult a
reputable professional for their solid advice before making a significant decision. They will guide you to make an informed decision about your choices.
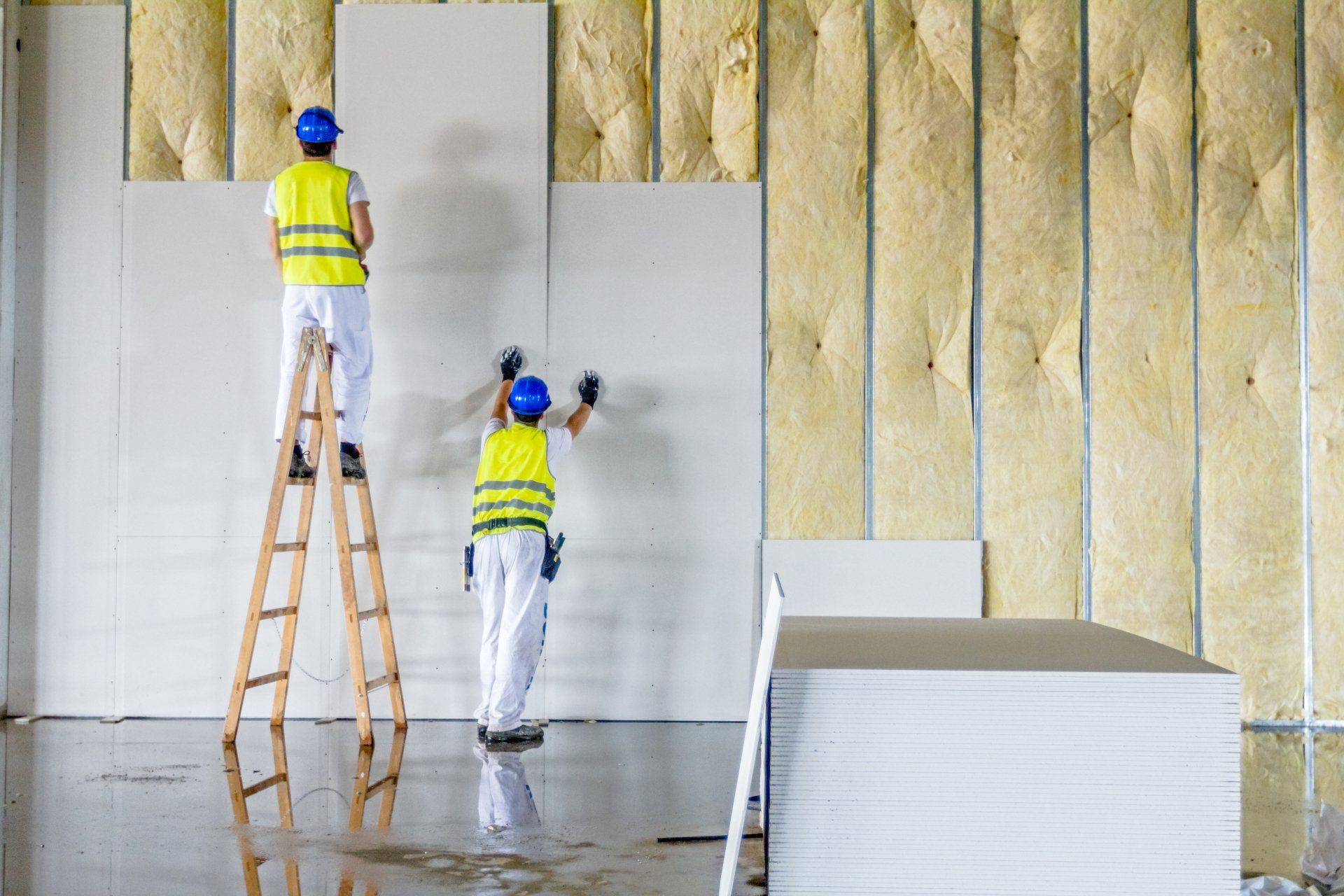