What's the Difference Between Type X and Type C Drywall?
The Difference Between Type X and Type C Drywall
Whether you are set to renovate your home or just furnish a newly required house and are very particular about the fire safety of it, then you need fire-rated gypsum panels. When it comes to this fire-retarding and resisting panels, the two names that come to mind are Type X and Type C. Both of them do the same job, but you will have to choose either of the two because you cannot use both of them. In the same vein, you cannot just relieve the work to drywall contractors in Orange County because the choice is yours to make at the end of the day—it's not even about them installing the wrong panels for you.
This article focuses on enumerating the key differences between Type X and Type C drywalls.Before examining and exploring the key differences between Type X and Type C drywalls, let us delve into what these two types of fire-rated gypsum panels are.
Type X Drywall
Type X Drywall is chiefly made from non-combustible glass fibers gypsum. What this means is that the elements and components from which Type X panels are made are resistant to fire to a reasonable extent. The materials utilized for Type X drywall can stand fire for up to 60 minutes before giving in. This makes Type X drywall a very good choice for projects like stairwell walls, shaft walls, area separation firewalls, etc.
Type C Drywall
Type C drywall is always better and more durable than Type X drywall. You can see it as a more premium version of Type X. It is made up of more non-combustible glass fibers, meaning more fire resistance. Apart from that, it utilizes the presence of a mineral called vermiculite which further increases its resistance to fire. On a general note, Type C drywall has a fire-resistant rating of up to 4 hours.
You can find any of these products at local drywall and insulation stores in their different thickness, i.e., 1/2" or 5/8". If you are confused, drywall contractors in Orange County can put you through and even help you out with a better selection if need be.
The Differences Between Type X and Type C Drywalls
From the explanations above, it is deductible that one key difference between Type X and Type C drywalls is that Type C is more resistant to fire than Type X. But there are even more differences.
Type C has More Thickness Options than Type X
On a standard note, Type X comes with a thickness of 5/8" while Type C comes with a smaller thickness or just about the same size as Type X. This means two size options for Type C. However, there are some drywall and insulation companies that offer Type X with a thickness of 1/2". Have it in the back of your mind that it is very rare to get it, especially if you plan to patronize your local stores. You will get better luck leaving the job to drywall contractors in Orange County like us.
Type C is an Enhanced Version of Type X
Because of the more fire-resistant ability of Type C, it is common to hear people call it a premium version or a more enhanced version of Type X. The truth is they are right. In fact, Type C is an enhanced version and premium version of Type X.
Type C has More Glass Fibers
It goes without saying that Type C gypsum panels are made from better and more non-combustible glass fibers, and that explains why it is more fire-resistant than Type X. While Type X can retard fire for up to an hour, Type C can do the same for up to two to four hours.
Type C can Replace Type X Panels, but not Vice Versa
Usually, drywall installers can substitute 5/8" Type X panels with Type C panels of the same size in most designs. Therefore, in scenarios where installers run out of Type X panels, Type C gypsum panels can come in handy. Please, note that Type X panels can NOT replace Type C panels in a design that is specifically made for Type C panels unless you are ready to compromise quality and safety.
Type X is Standardized
While Type X panels pass through the American Society for Testing and Materials for quality and standard tests before being released to the market, no such standard tests are in place for Type C panels at the time of writing this post. This is one reason why you need the services of professional drywall contractors to know which product to settle for.
Type C Panels Perform Better when Installed Horizontally
Type C gypsum panels with the thickness of 1/2" are a better option for ceiling projects. This is because they perform better when they are installed horizontally. Therefore, vertically installing Type C panels does not offer the same level of fire rating.
Type C Panels are Typically Thinner and Easier to Install
Type C panels can be as thin as half an inch, making them easier to install.
Type C is More Expensive
With all the advantages Type C panels have over Type X panels (thinner, easier to install, better fire rating, etc.), it comes as no shocker that they are more expensive.
Type X Panels Last Longer than Type C Panels
If there are no eventualities of fire outbreaks, Type X panels usually outlast Type C panels.
Drywall Contractors in Orange County
Do you need the services of drywall contractors in Orange County? If yes, then we are the ones you are looking for. We are a reputable and professional team of drywall contractors that can help you with everything related to drywalls. With us, you can bother less about drywall installation, finishing, and maintenance. Our competent team of contractors can help you choose the best product for your housing needs.
We are very professional, swift to action and trustworthy. Contact us today to enjoy our quality services. We promise that you won't regret doing so.
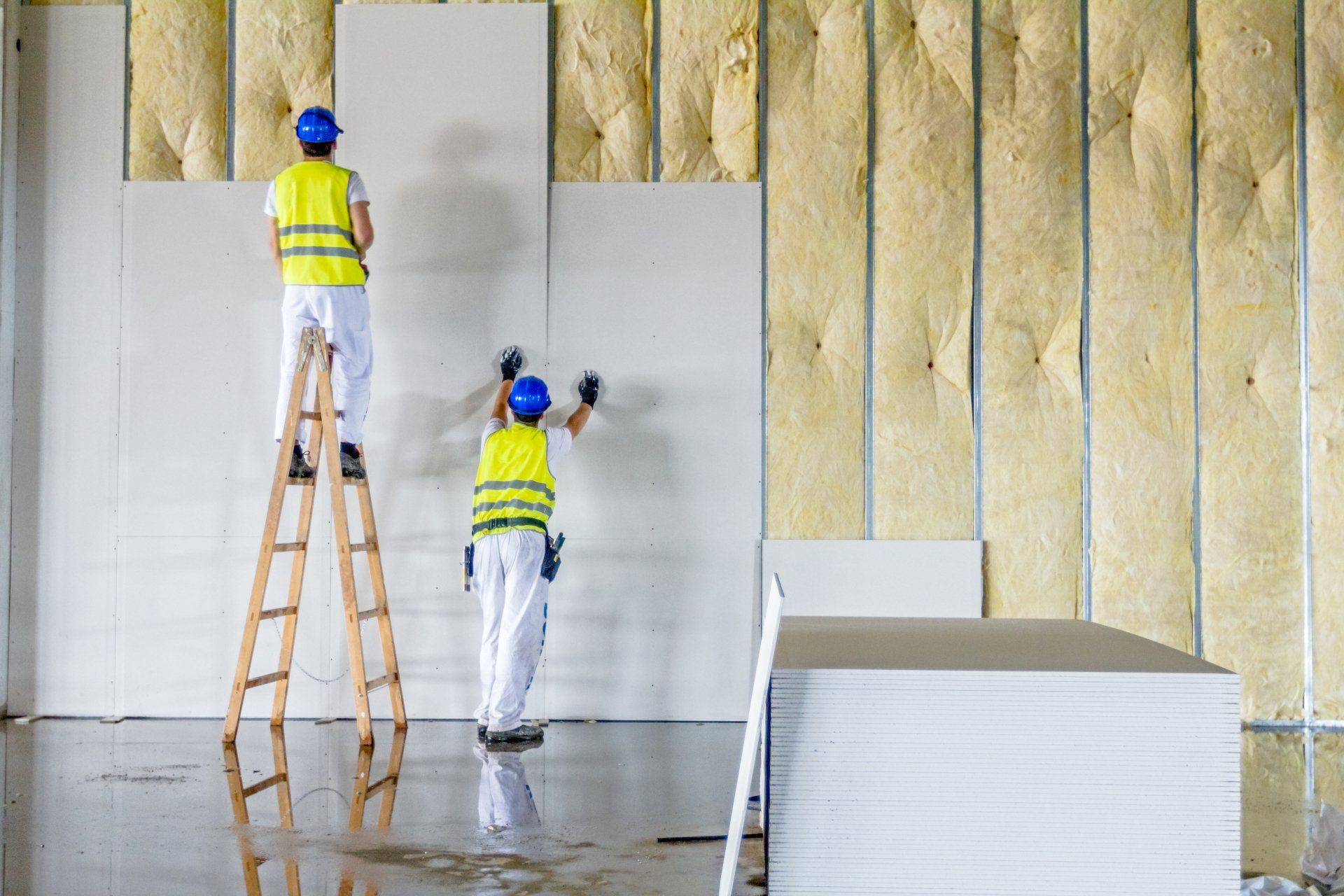